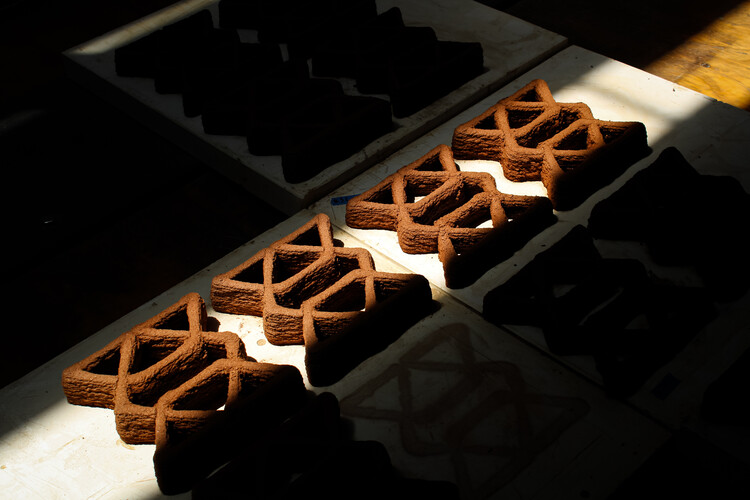
Carved stones were the first tools that hominids used to transform their environment. It is exciting to imagine how, since the Stone Age —a period that began approximately around 10,000 BC— and thanks to humanity's long evolutionary process, the tools we used have evolved from simple stones to complex robotic systems. These advancements represent a revolution in production methods, both at the current industrial level and on a local scale.
Technologies such as artificial intelligence (AI) and digital fabrication systems have been perceived as labor-replacing threats varying by context. In Latin America, manual fabrication is deeply ingrained, specialized, and cost-efficient in some sectors, making digital substitution less pressing. In contrast, biomaterials derived from fungi or agro-waste provide environmentally friendly construction alternatives, promoting sustainability and circular economies. This stimulates meaningful discussions about the potential of digital fabrication, requiring an understanding of local resources and challenges. Therefore, it lays the groundwork for biomaterials that preserve identity while offering solutions to local issues.
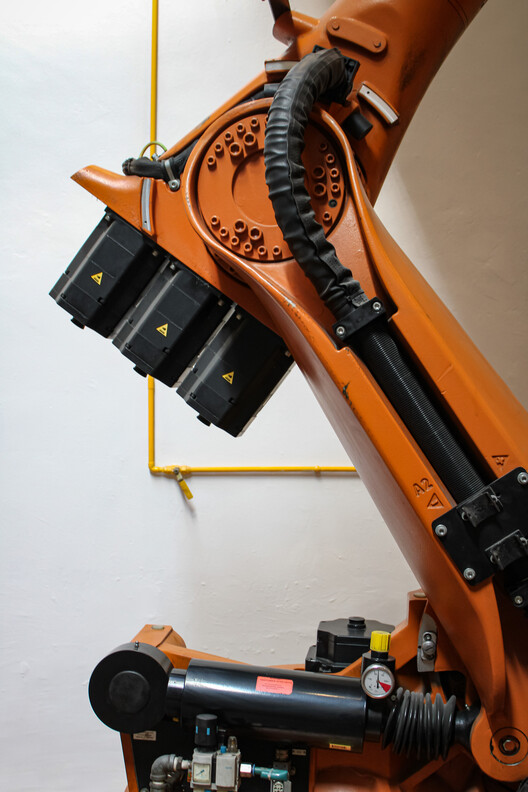
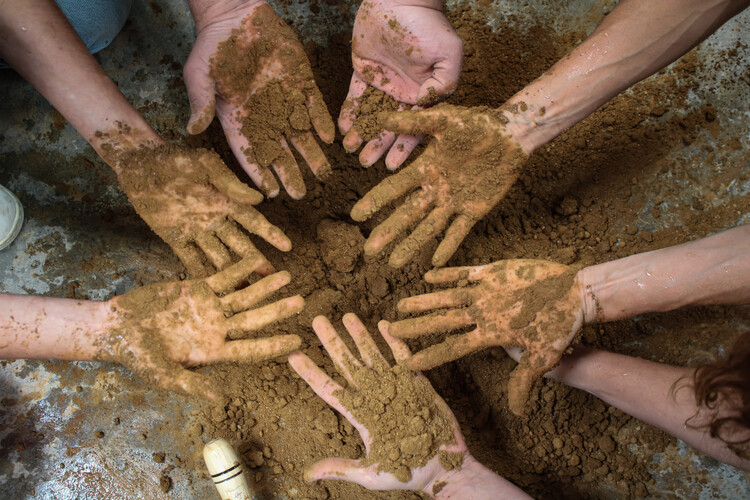
Whether organic or inorganic, waste now demands attention as an indispensable resource. Consequently, initiatives like Manufactura integrate digital fabrication and waste utilization for fresh perspectives. Dinorah Martínez Schulte, the co-founder of this project, gave us insights about the potential of these processes and their application in a material such as wood, which has been used since our ancestors began to shape other materials with stone.
Contextualizing materials and understanding their origins
According to Martínez Schulte's research in Mexico, annual wood production reaches approximately 8 million m³. Of this volume, 70% goes to the sawmill industry, which generates around 2.8 million m³ of waste, mainly sawdust, chips, and bark. Although there are currently ways to manage wood waste, they depend on chemical processes and fuels.
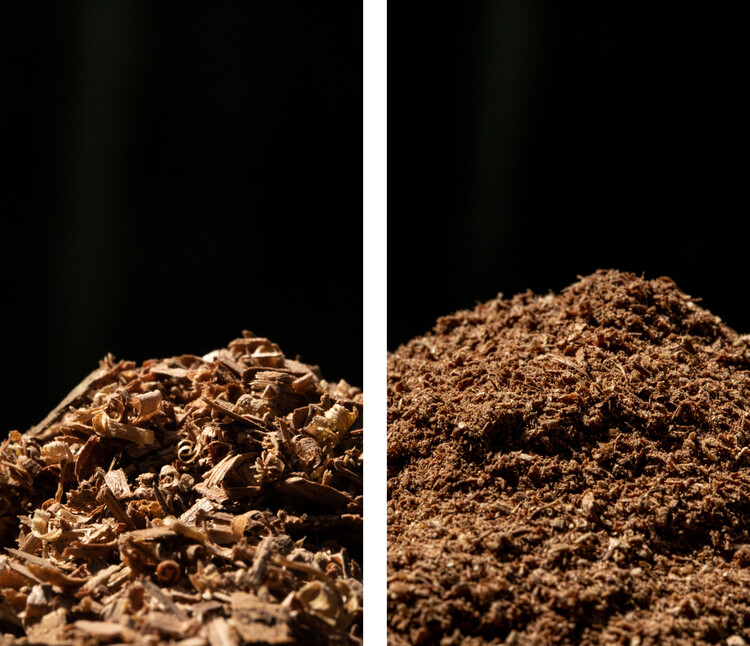
"The Wood Project / Un Proyecto de Madera" is a research initiative carried out in collaboration with La Metropolitana, a local workshop that combines traditional techniques with technology in its furniture manufacturing processes. Addressing a daily issue, the project repurposes sawdust —usually discarded— summing up around 5-6 bags, roughly 40 kg each, generated daily. This not only mitigates waste but also addresses safety concerns due to sawdust's flammability and respiratory risks when airborne.
Although this wood waste by itself is not highly polluting, the volume that is discarded does represent a considerable source of raw wood, and in regions of Mexico, it has a high economic and cultural value. As part of this project, Manufactura created a bio-composite based on sawdust residues from the Tzalam tree (Lysiloma latisiliquum). This species is native and highly appreciated in the southeast of Mexico, in the Mayan region, due to its appearance, high resistance, and aesthetic characteristic of reddish color and pronounced veins.
Chemistry as part of the manufacturing process
In the manufacture of bio-composites, Manufactura proposes an approach that first comprises the chemical composition of the materials. From their first projects working with eggshells, they approached the material by considering it as calcium carbonate and, as in the case of wood, as cellulose.
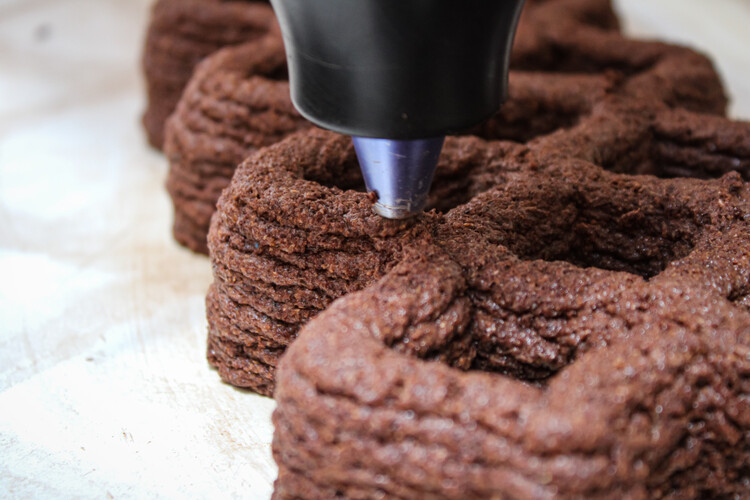
After conducting several experiments to generate a cellulose-based mixture, they discovered that sawdust undergoes changes in its physical state related to binding and drying, depending on the machine from which it is extracted. In addition, moisture in the biocomposite was conducive to fungal growth, so they experimented with lime and gypsum to neutralize it. Also, after developing several prototypes, they determined that the sawdust from the calibrating machines and the CNC router had the optimal physical conditions to allow the 3D printing process.
Chemical composition is the basis of everything. -Dinorah Martínez Schulte
The transition from a subtractive manufacturing process to an additive one led to the exploration of new approaches. To manufacture the modular tiles from the bio-composite, it was necessary to understand the weight, density, and water content of each material. In addition, organic binders were used as a matrix, along with lime, which, after several tests, proved to be more effective in preventing fungal growth.
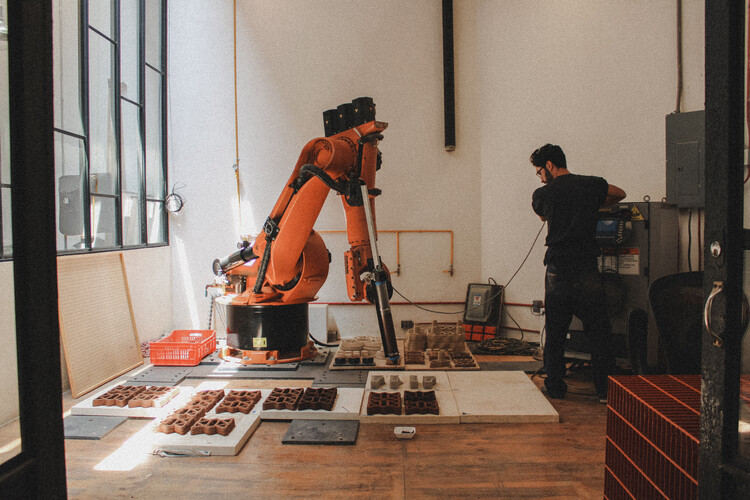
In this research process, they worked in collaboration with the Laboratory of Materials and Structural Systems of UNAM, which provides a scientific perspective to the project. Finally, after numerous processes and tests, a material for casting combined with a binder is obtained. This material is then converted to a plastic state using an extruder designed for semi-liquid materials, which is mounted on a robotic arm.
Neo-wood and geometry
In testing, Manufactura observed that the pieces retained properties of the wood species used. The first pieces manufactured using pine waste were less rigid and lighter in color compared to those made with tzalam, which showed greater hardness and a reddish color. In both cases, these qualities were similar to those of the wood in its original state. The interplay between the mixture, technical printing parameters (extrusion speed and robotic arm speed), and the shape of the pieces resulted in the realization of three lattices; 72 pieces, each measuring 20 x 20 cm. This 3-week printing and drying process yielded replicable pieces that can be assembled for scalability. Martínez Schulte highlights the need to consider variables like temperature and humidity, which affect material printing. Parts typically dry within 5 to 7 days.

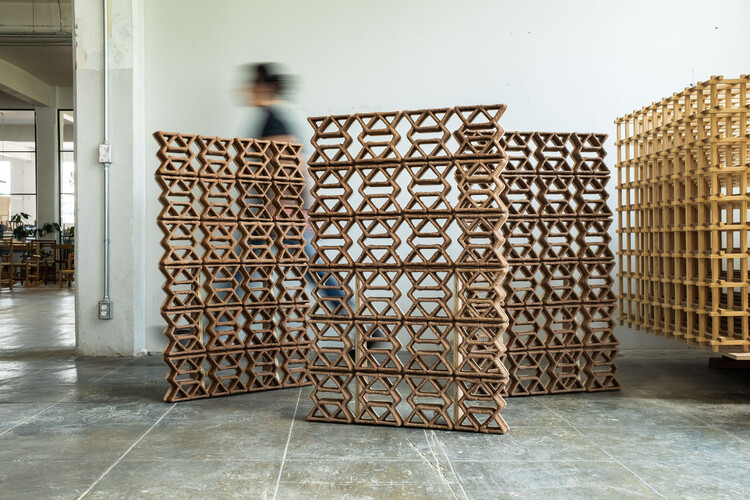
To determine the shapes of the pieces, several prototypes were created, beginning with basic geometries like circles, squares, and triangles. This approach helped identify the most suitable geometry. Martínez Schulte emphasizes that by testing different geometries, a better understanding of the material is achieved. As a result, it becomes possible to define the sizes of the pieces, reduce the distances, and identify where an infill pattern is necessary.
Digital fabrication is not linear, it is an infinite loop. -Dinorah Martínez Schulte
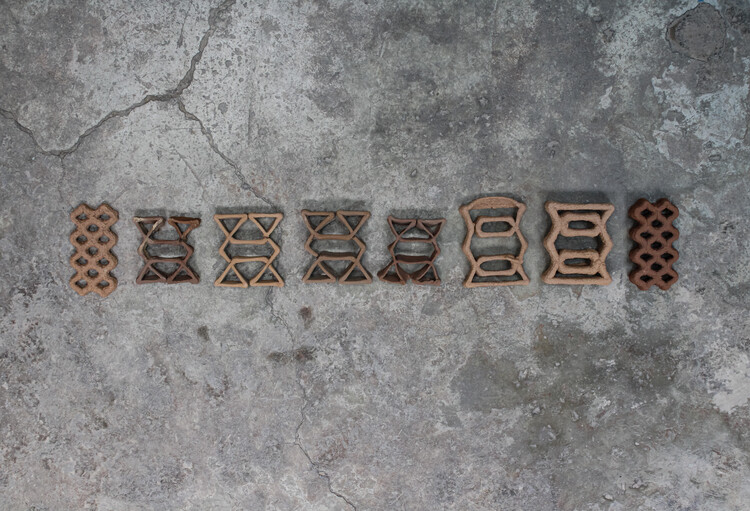
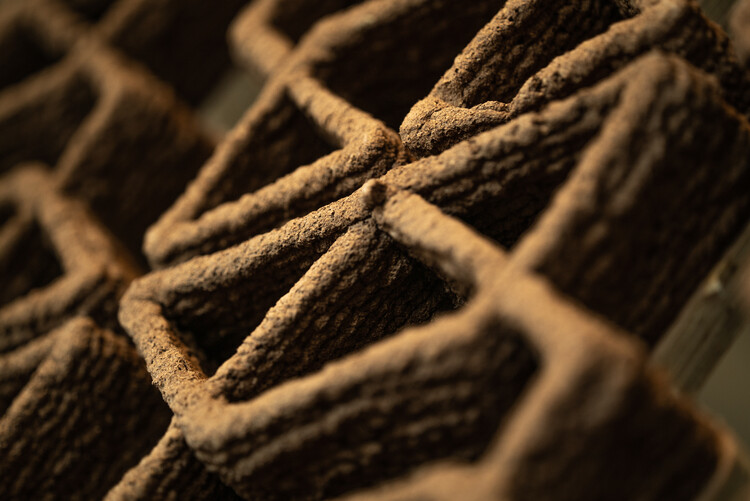
In summary, the realization of this project has been feasible thanks to the synergy between computational design, the advantages provided by digital fabrication, innovation in the local context, and creativity in converting wood waste into new materials. It also highlights the importance of thinking about bio-materials and digital fabrication as a way to address local issues and generate new conversations based on the technical and aesthetic qualities and applications of bio-composites. Whether in the professional sphere through work in the workshop or from the academy collaborating with universities, Manufactura and Dinorah Martínez Schulte propose a change of perspective on what is considered waste.
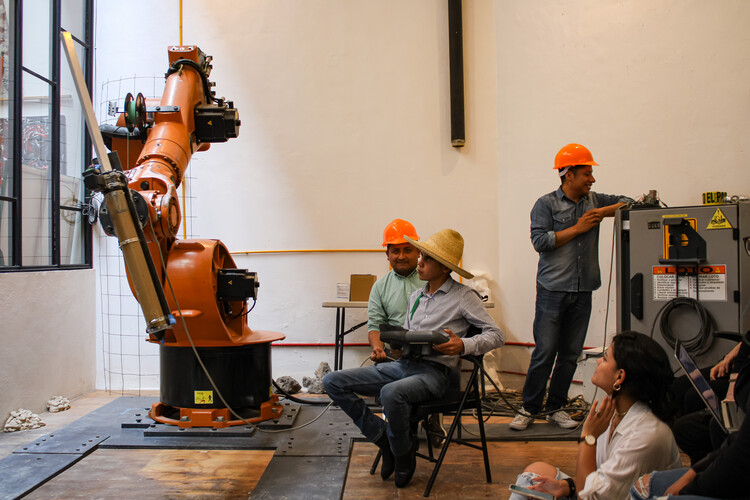
The impact of digital fabrication and biomaterials is being answered in the different proposals emerging at a global scale, especially regarding the potential benefits and risks involved. One fact is that these types of materials are making their way by challenging contemporary architectural production as well as current manufacturing methods in favor of a circular economy. As Carlos Raúl Villanueva stated: “Architecture is a social act par excellence, utilitarian art, as a projection of life itself, linked to economic and social problems, and not only to aesthetic norms…”.